Join the MASU Family | Enjoy 10% Off Your First Order | Use Code: 10off
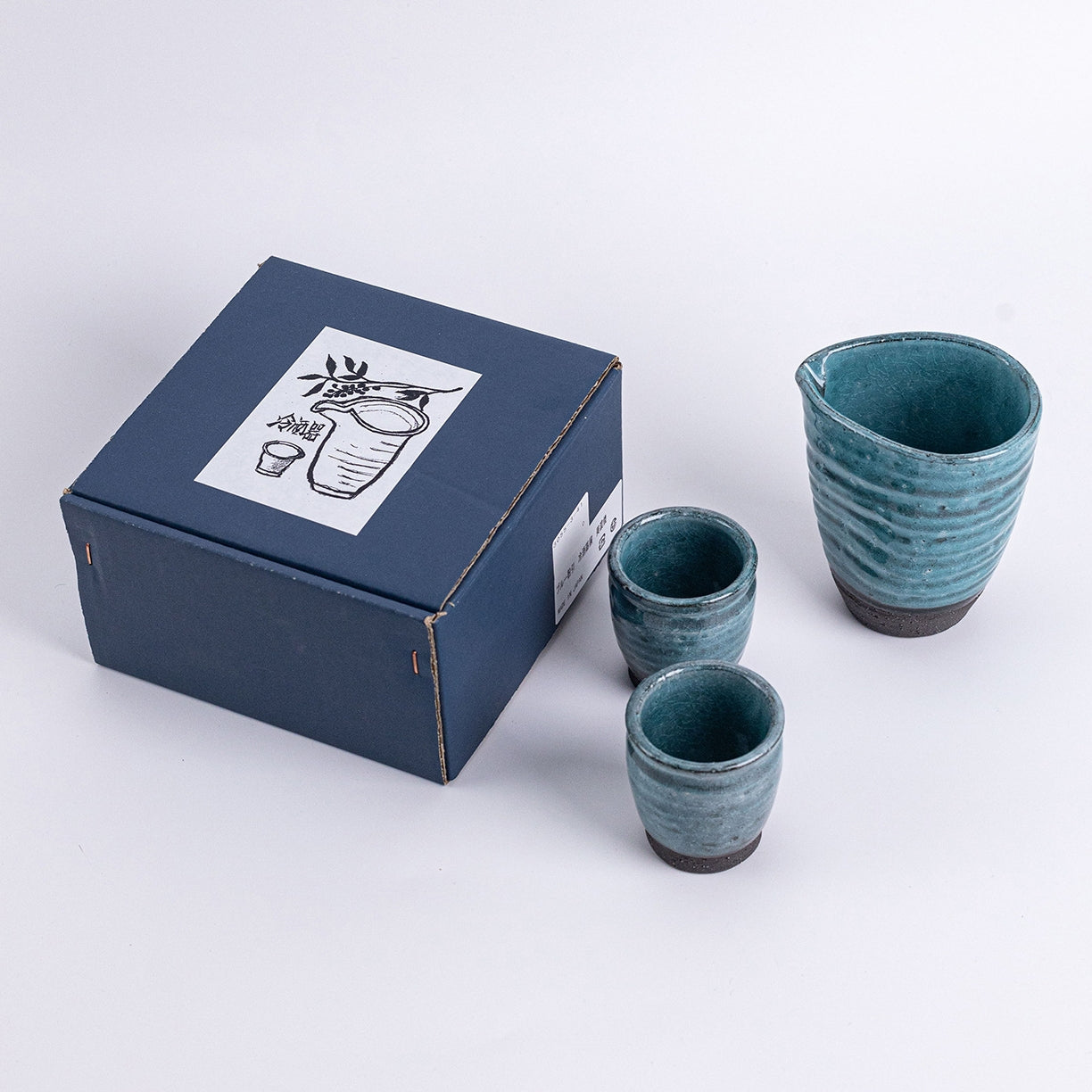
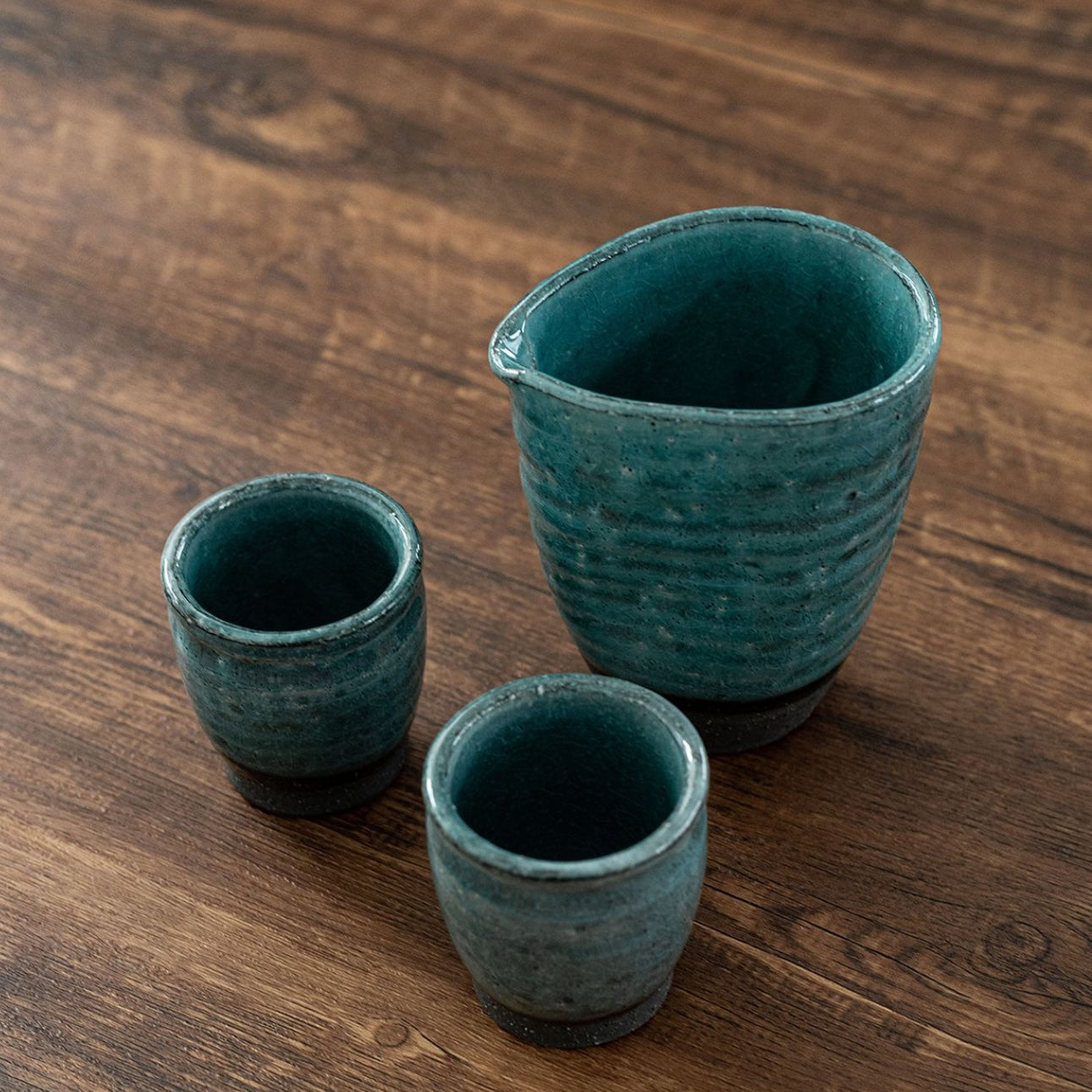

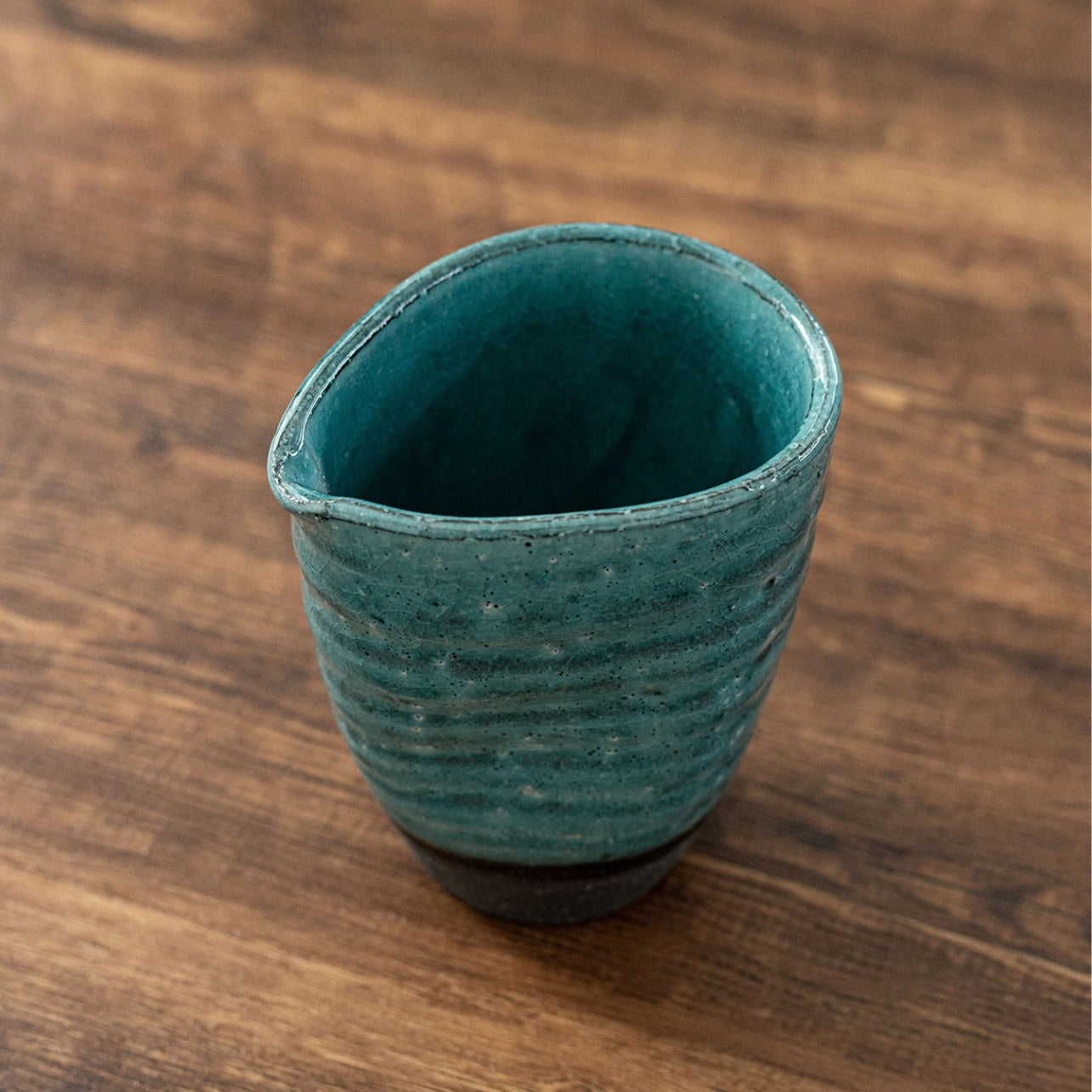
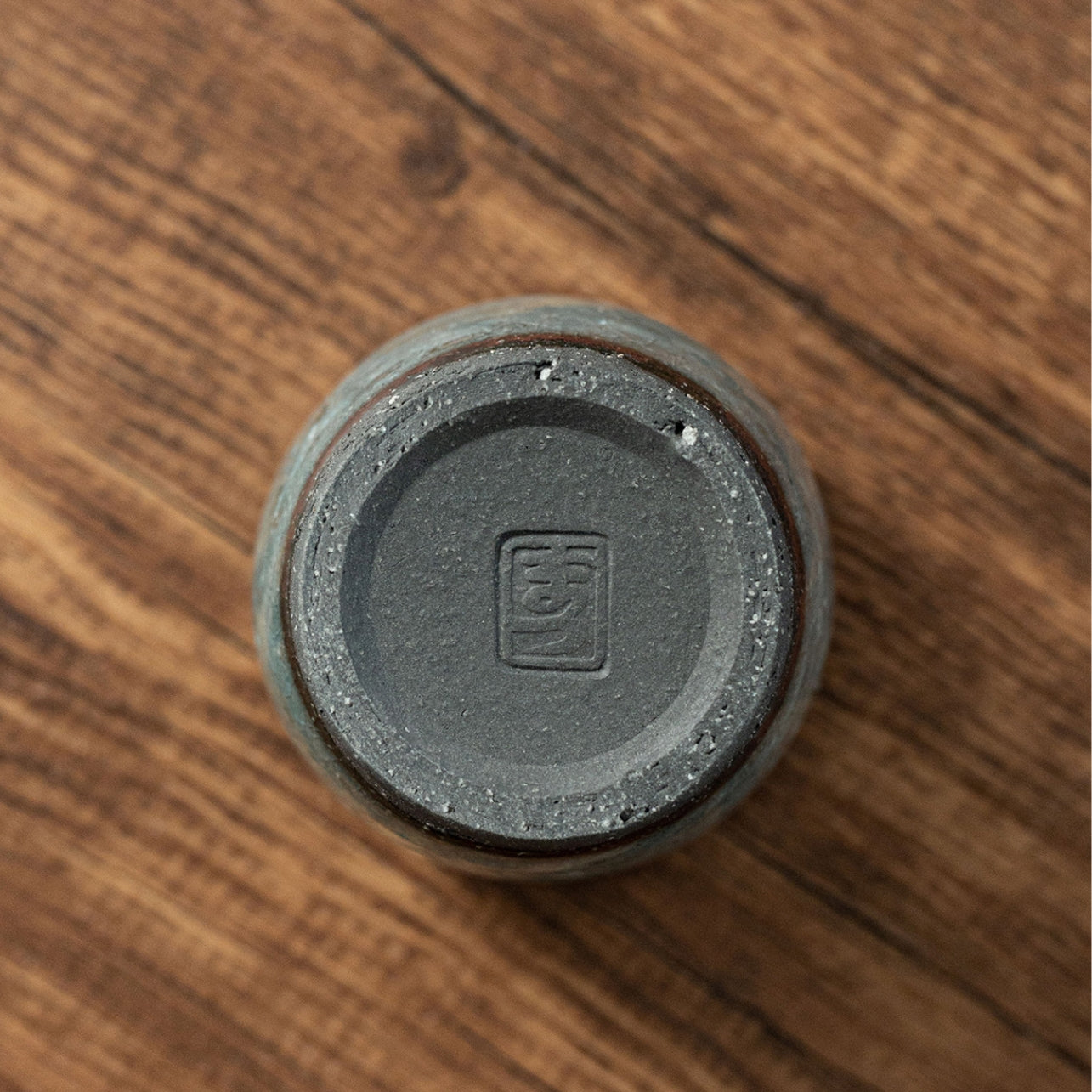

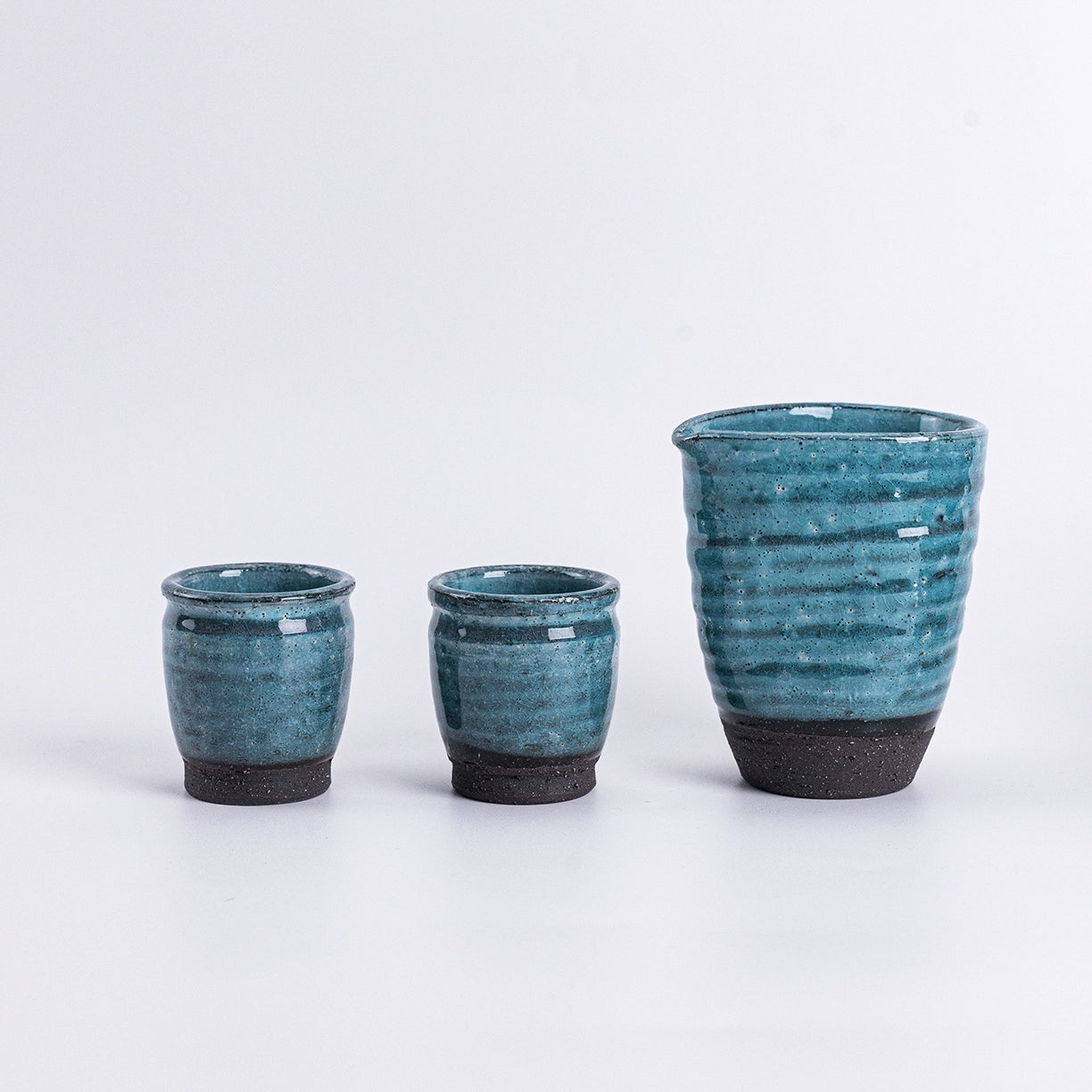
Hatsuichi Mino Ware Blue Pine Sake Set
The Hatsuichi Mino Ware Blue Pine Sake Set embodies elegance and a serene Japanese aesthetic. Crafted with traditional Mino ware techniques, the set includes a sake flagon and two sake cups, each finished in a soft, ocean-inspired blue glaze that evokes the feeling of calm waves. The cups are adorned with a subtle, ice-cracked glaze pattern, adding a touch of organic texture and warmth to the smooth surface, making each piece unique.
The set’s pottery embodies craftsmanship and thoughtful design, providing a comfortable grip and a smooth, jade-like texture. Its rich blue color, symbolizing tranquility and romanticism, invites a sensory experience reminiscent of the deep sea. This carefully designed set makes it ideal for sharing a drink with friends or enjoying a quiet moment alone.
• Origin: Made in Japan
• Craft: Mino Ware
• Product:
2x Sake Cup
1x Sake Flagon
Handcrafted in Japan with traditional ceramic-making methods, each with a unique design and texture.
Materials
Specifications
Product Care
Shipping
Times
Orders take 2-3 business days to process after placing the order before shipping out.
Standard Shipping Times
• North America
United States (Mainland): 5 - 12 days
Alaska, Hawaii, and other US regions: 10 - 20 days
Canada: 5 - 14 days
Mexico: 10 - 17 days
• Europe: 5 - 12 days
• Australia/New Zealand: 6 - 14 days
• Asia
Southeast Asia: 5 - 8 days
Other Regions: 5 - 14 days
• Latin America: 10 - 20 days
• Other Countries: 10- 20 days
Express Shipping Times: 4 - 8 days
Available for Selected Products in the Following Countries:
• United States(Mainland)
• United Kingdom
• France
• Germany
• Italy
• Austria
• Spain
• Netherlands
Priority Shipping Times: 3 - 5 days
Available for Selected Products in the Following Countries:
• United States(Mainland)
• Canada
• United Kingdom
• France
• Germany
• Italy
• Austria
• Spain
• Netherlands
• Australia
• New Zealand
• United Arab Emirates
• Saudi Arabia
Return, Refund & Exchanges
We offer a 7-day return & exchange policy. For detailed information Return, Refund & Exchanges
Choose options
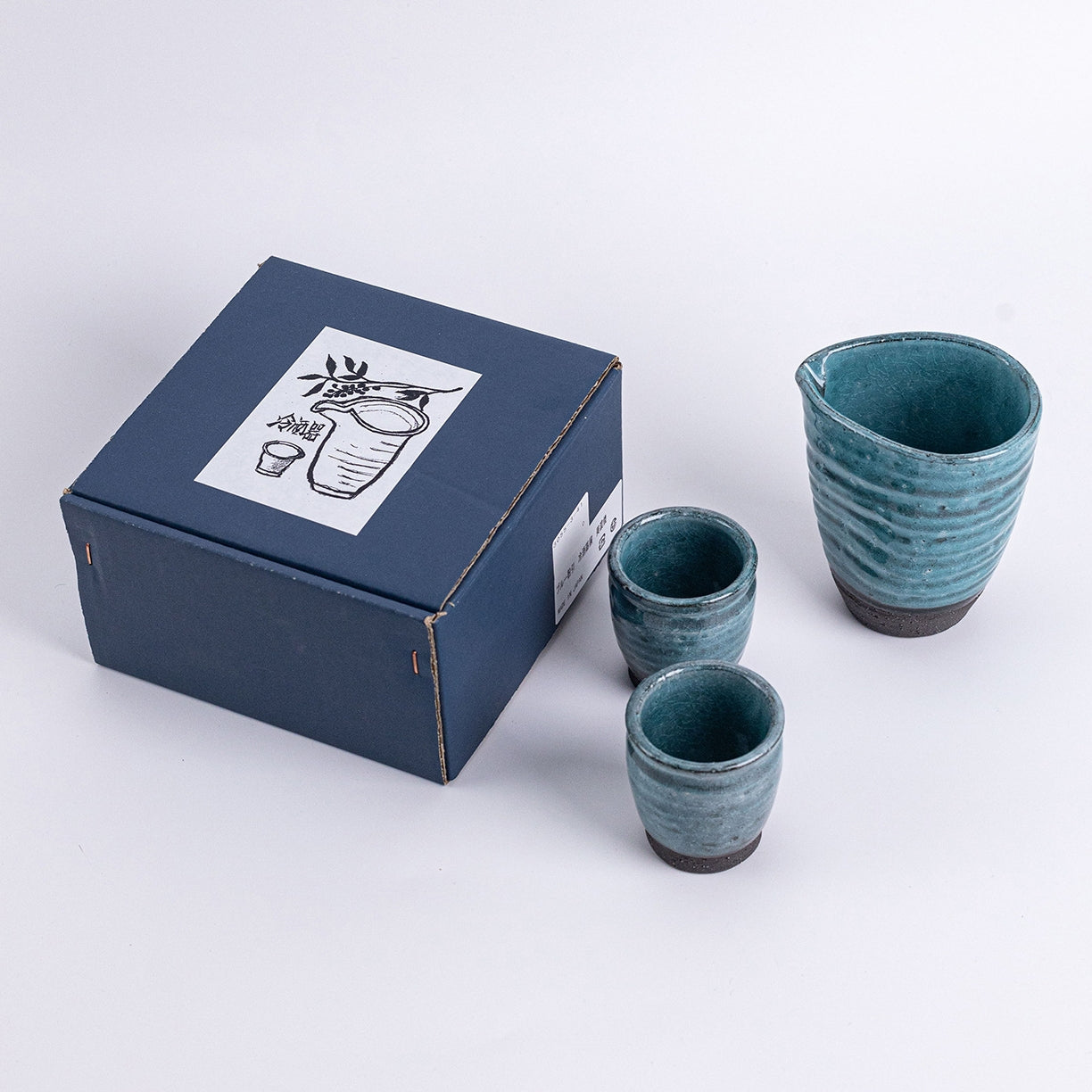
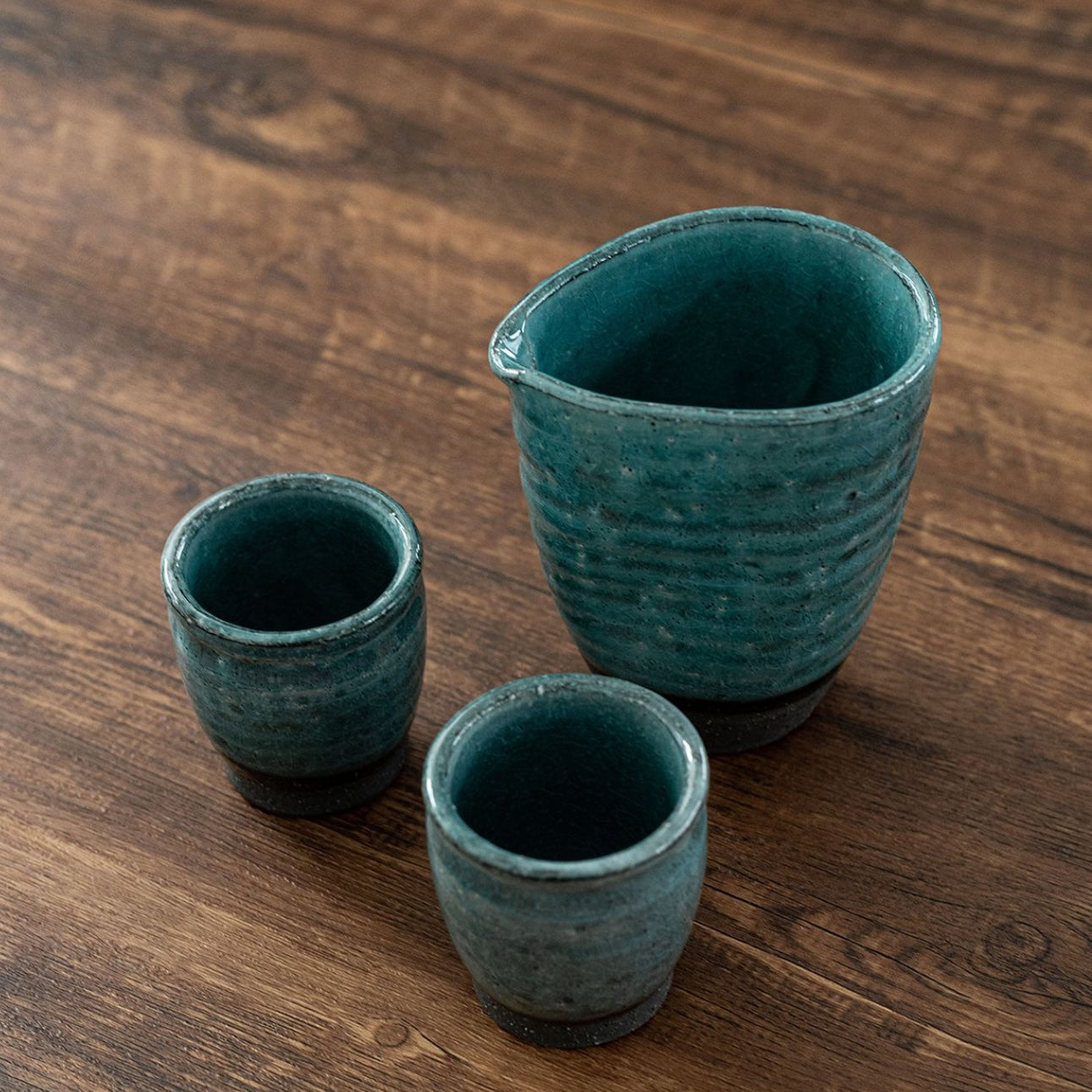

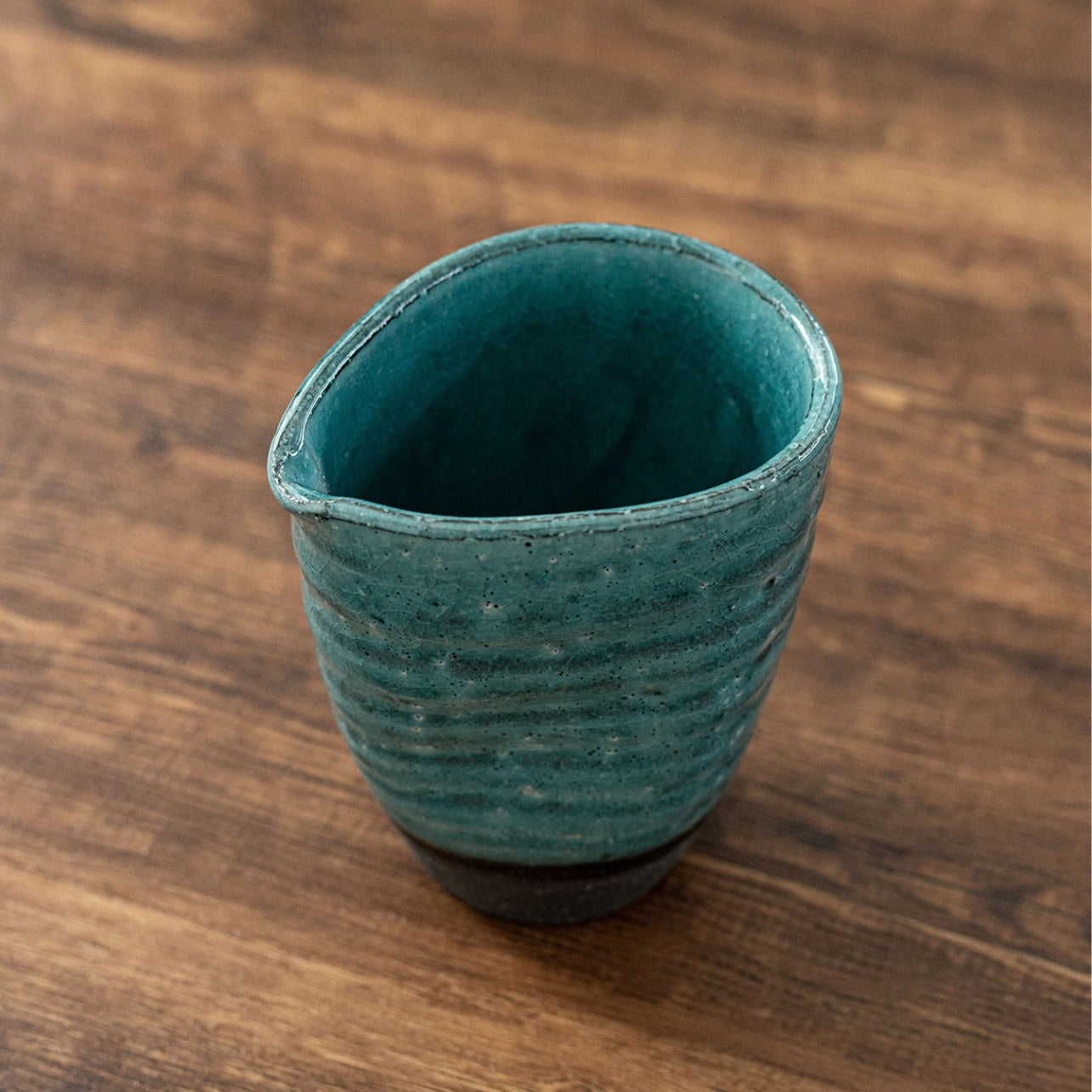
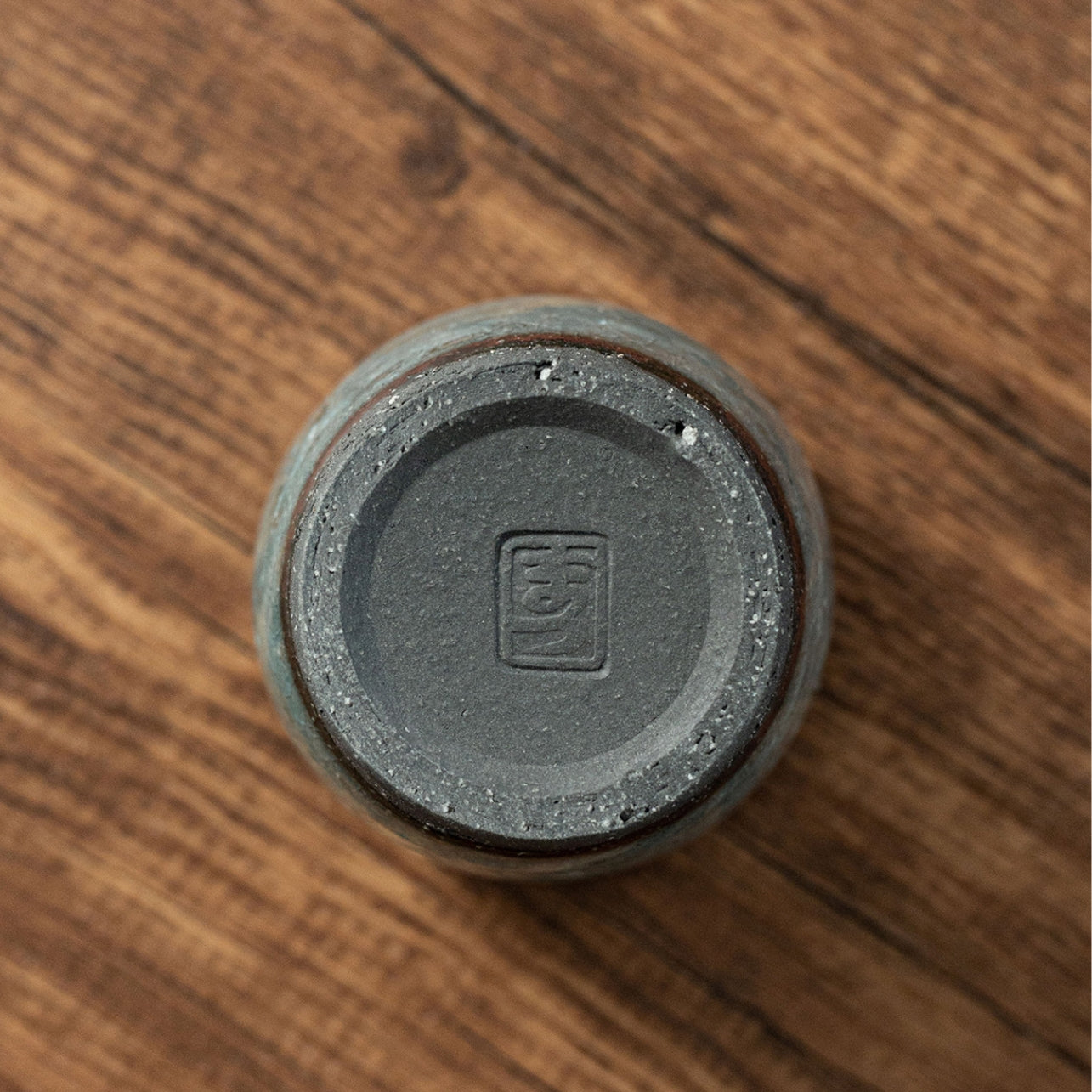

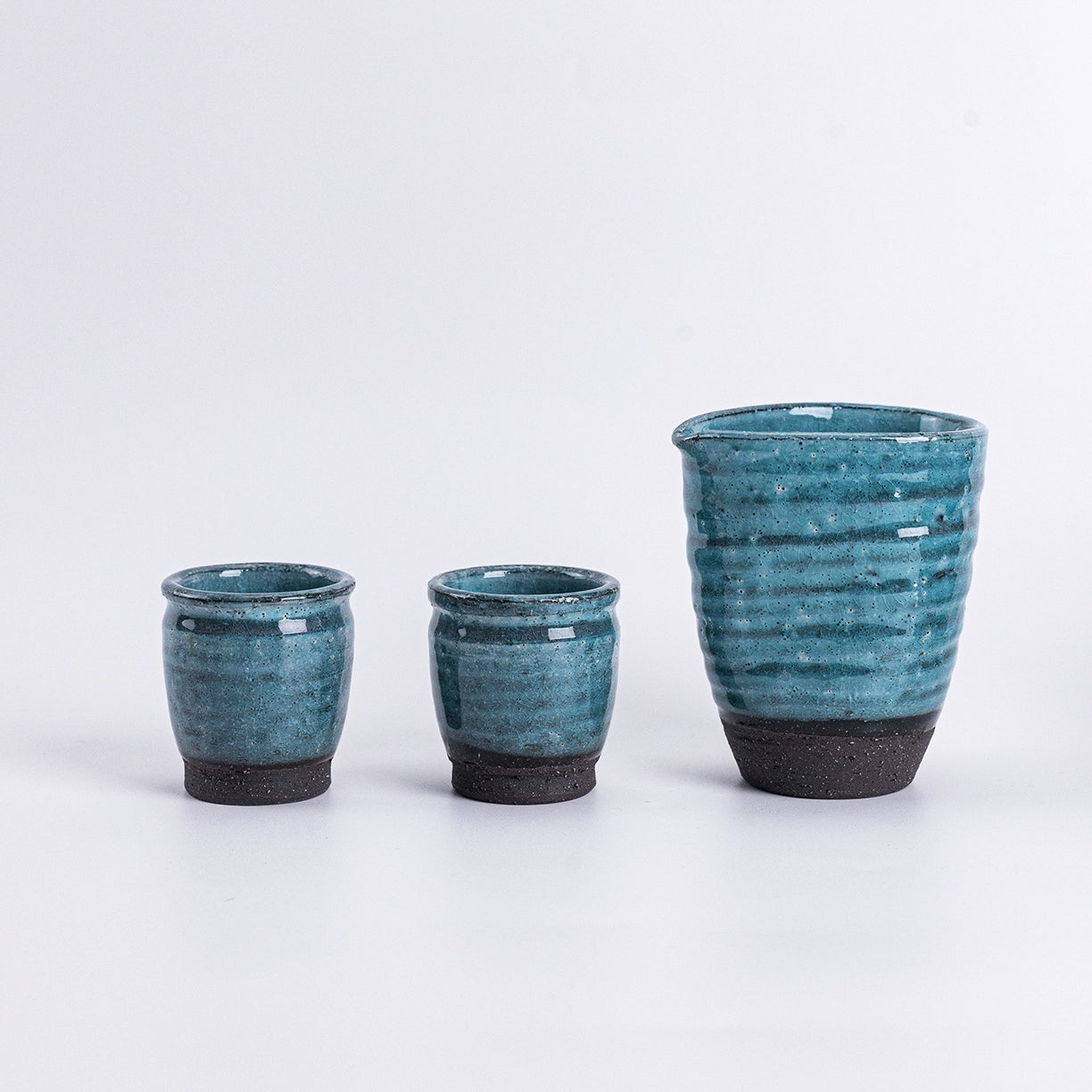
Mino Ware 美濃焼
Production Process
全行程に手間ひまをかける。そのこだわりが和の逸品を生み出す。
Great care and effort are devoted to every step. This dedication creates exceptional works of Japanese craftsmanship.
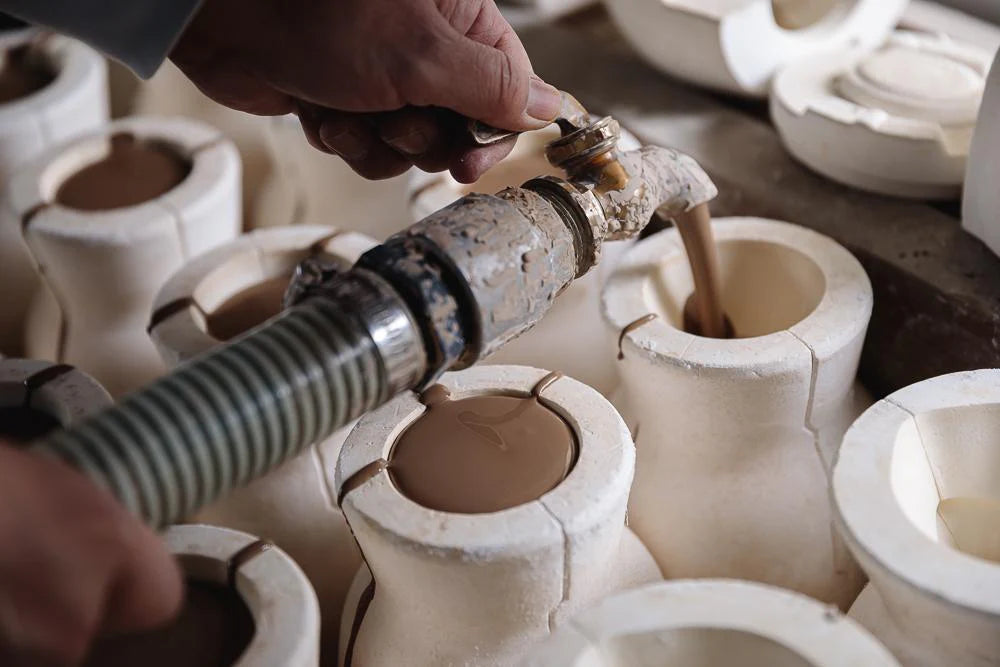
Molding/Gaba Casting
(ガバ鋳込み, Gaba-Ikomi)
The process begins by pouring clay slip, known as 泥漿 (deijou), into a 石膏型 (sekko-gata) or plaster mold necessary for shaping. The plaster absorbs the moisture from the clay, gradually solidifying it. After about 2 to 3 hours, once the clay has solidified to the thickness of the main body of the pottery, the excess clay is removed from the plaster mold. The act of discarding the clay in one go gives rise to the term ガバ鋳込み (Gaba-Ikomi).
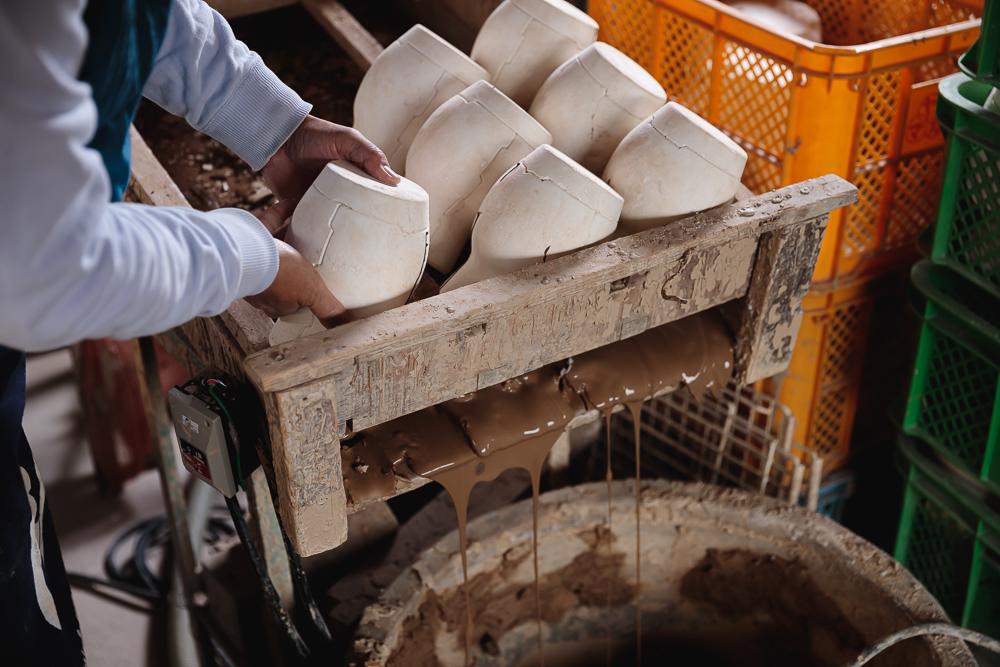
After leaving it in this state for about an hour, the excess clay is further scraped out manually, and finally, the formed contents are removed by opening the plaster mold.
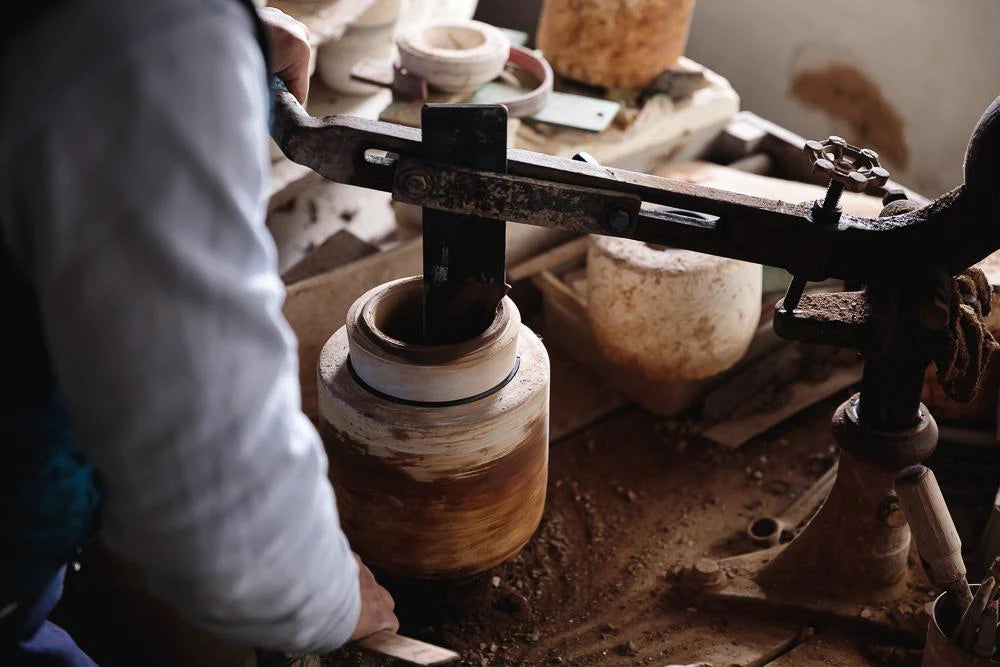
Molding/Powered Molding
(動力成形, Douryoku Seikei)
Another molding method involves using a powered wheel. In this process, a lump of clay is placed into a 石膏型 (sekko-gata) and pressed against the mold while a semi-automatic wheel spins at high speed to shape the clay.
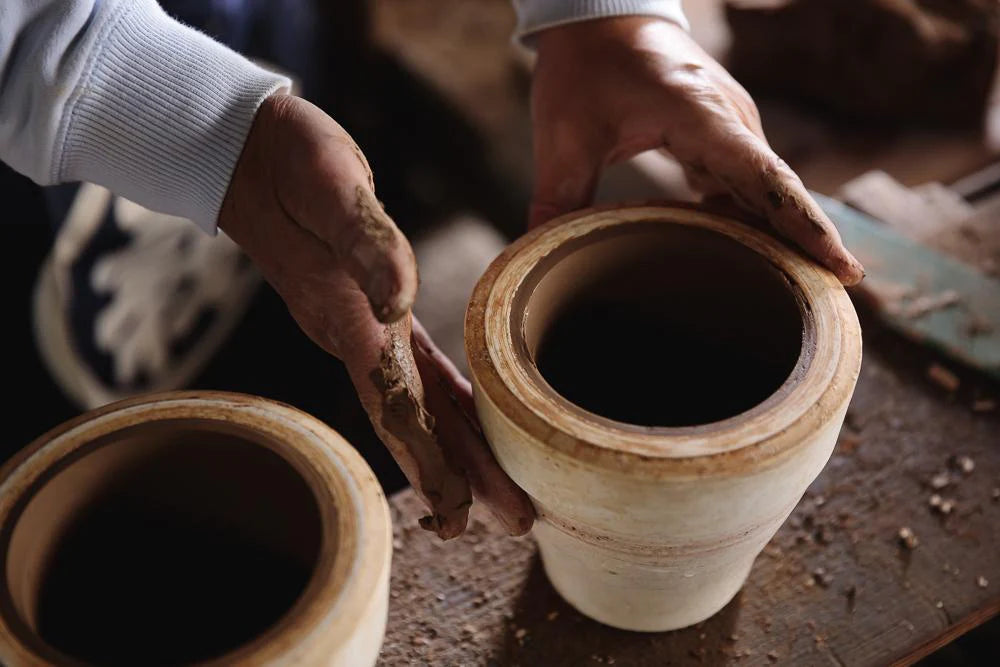
The molding of 磁器 (jiki) is done manually. Alongside ガバ鋳込み (Gaba-Ikomi), this is one of our fundamental molding methods.
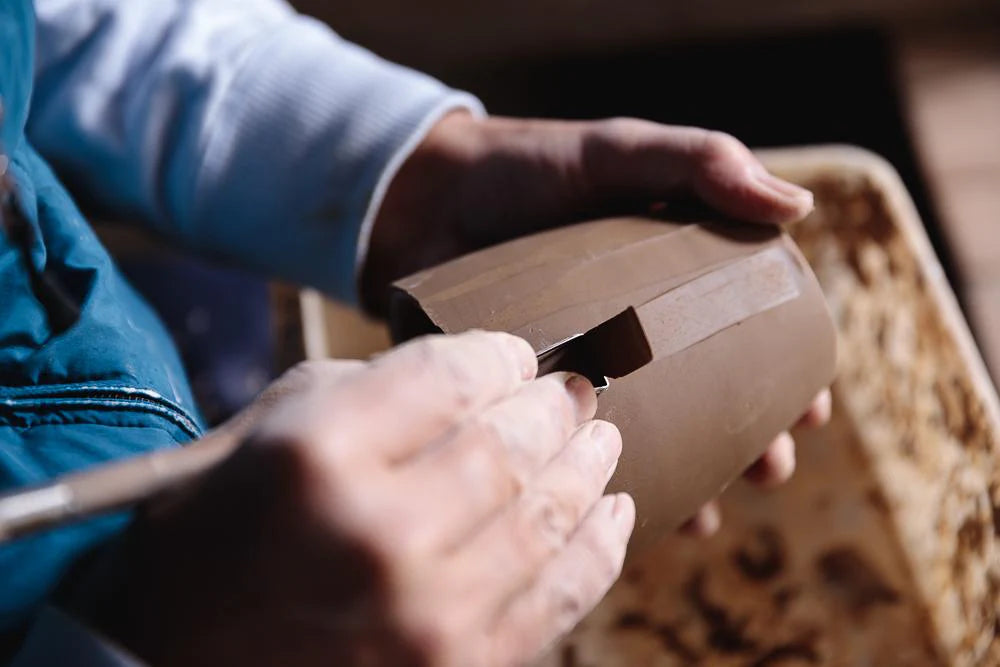
Molding 2/Decorating and Attaching Handles to Mugs
(マグカップの模様付け・取っ手取り付け)
After molding, the pottery is dried, and any excess parts are trimmed (バリ取り, Bari-tori). However, when making mugs, the process first involves a decorative technique called 鎬 (shinogi), which decorates the surface.

The 鎬 (shinogi) pattern is applied entirely by hand, making it a time-consuming process, but it is a crucial step that determines the design of the piece. After this, the handle is attached.
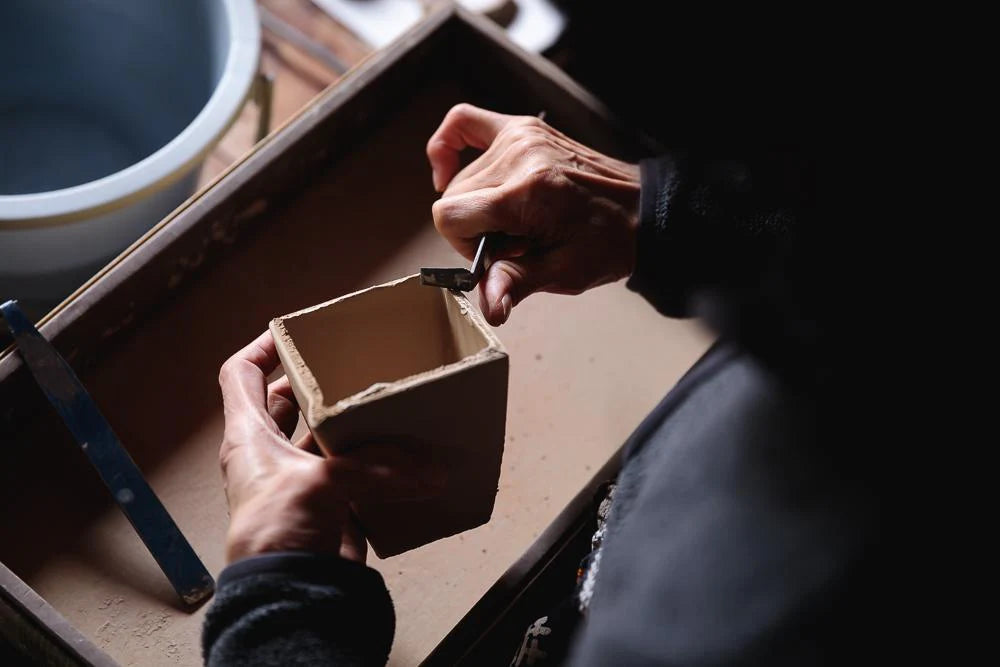
Trimming After Drying
(乾燥後の面取り, Kansou-go no Mentori)
Once dried, any unnecessary parts are cut off, and each piece is carefully wiped with water to complete the trimming.
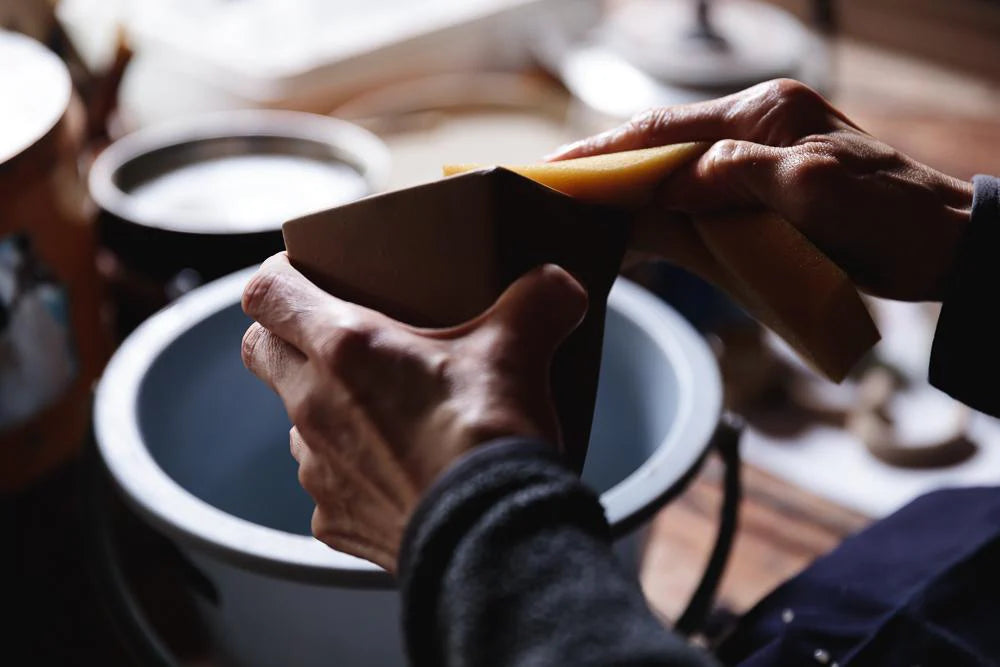
Although a simple task, if this step is neglected, burr lines may remain after firing, significantly affecting the final product, making it an essential process.
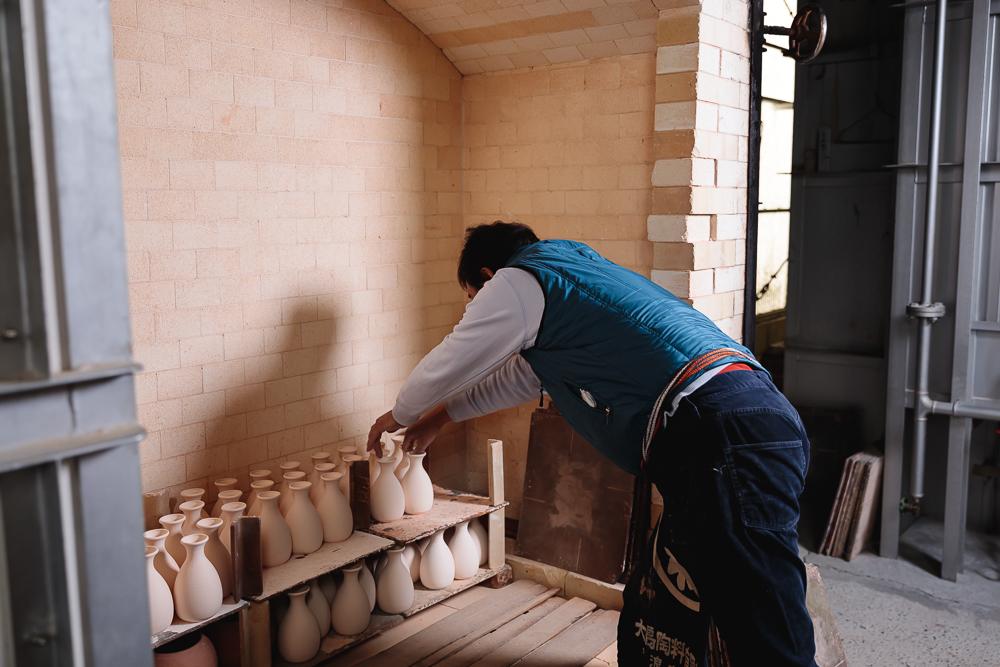
Biscuit Firing
(素焼き, Su-yaki)
After trimming, the pieces undergo biscuit firing (素焼き, su-yaki). This process involves firing the clay at a low temperature of about 800°C for approximately 6 hours to completely remove moisture from the material. This step allows for subsequent painting and results in a beautiful finish. After 素焼き (su-yaki), the strength of the pottery slightly increases, and it produces a dry sound when tapped by hand.
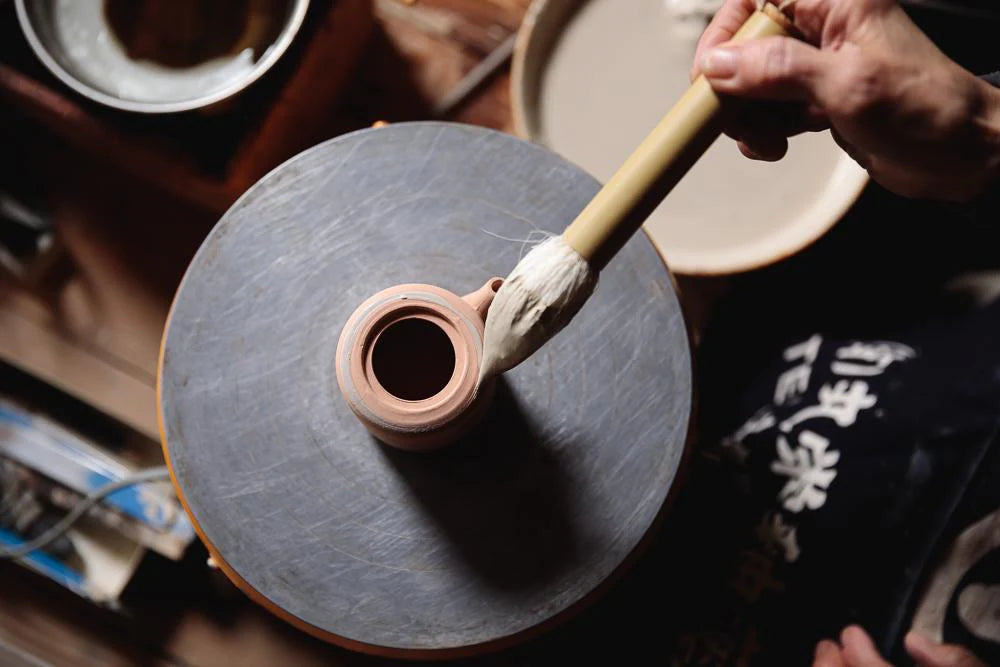
Underglaze Decoration/Brushwork
(刷毛目, Hakeme)
After 素焼き (su-yaki), the decoration process begins. One of the techniques involves using a brush to manually apply a coating called 化粧土 (keshou-tsuchi). Each piece is carefully and meticulously decorated over time.
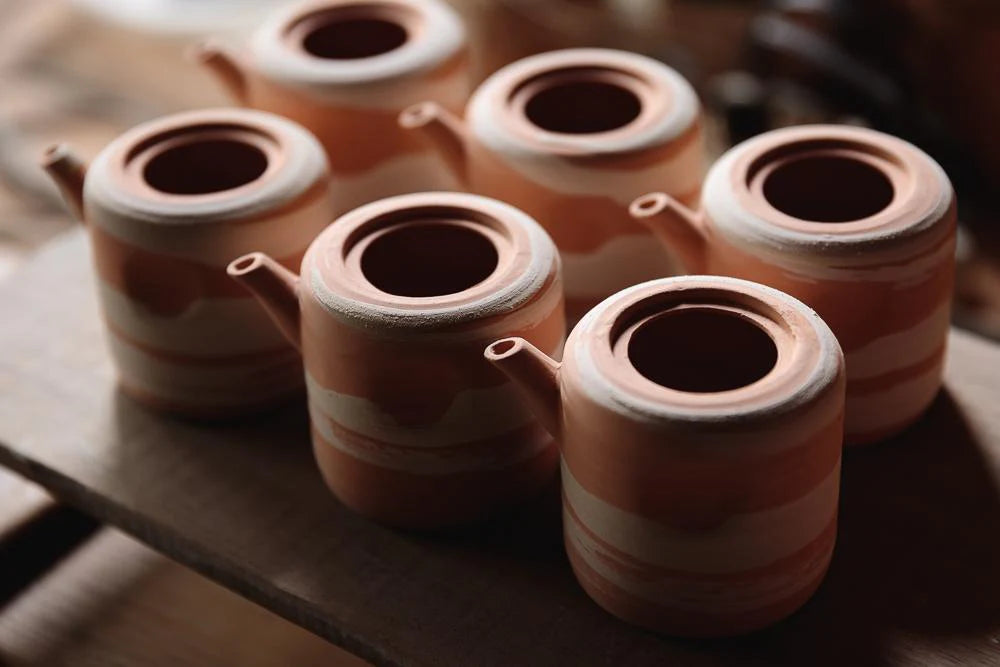
This technique is used to create a gradient effect on the surface after the white clay (白土, shiro-tsuchi) is applied and fired. The color variations that occur bring out a unique 侘び寂び (wabi-sabi) aesthetic.
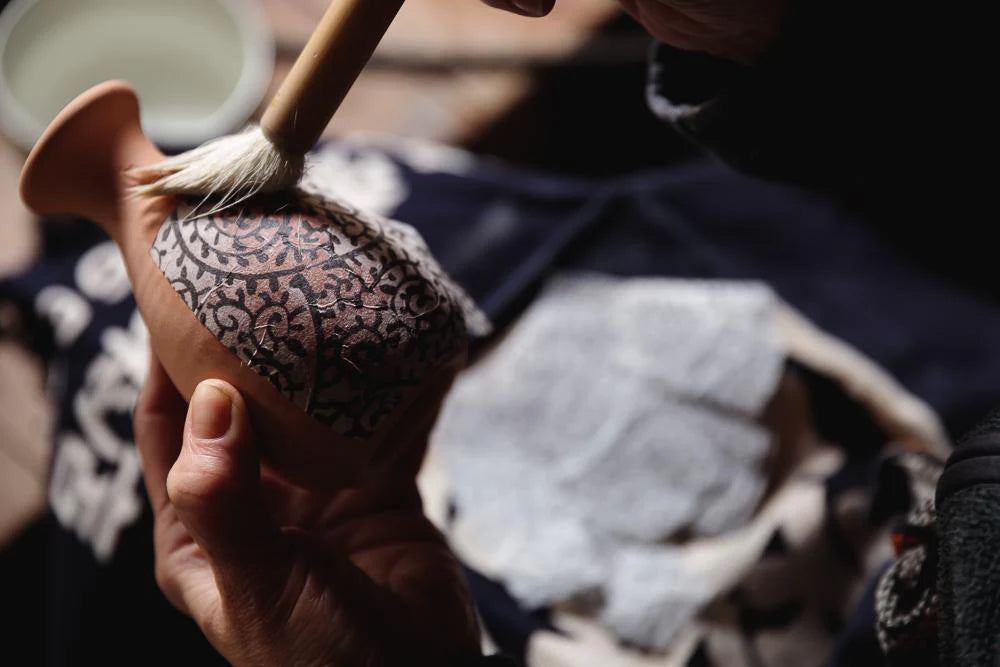
Underglaze Decoration/Copper Plate Transfer
(銅板転写, Douban Tensha)
The copper plate transfer technique involves engraving a design onto a copper plate (銅板, douban) with a stylus, rubbing paint like 呉須 (gosu) into the design, and then transferring the paint onto the surface of the ware using printed paper. This technique was refined in 美濃 (Mino) and perfected in 1889 (Meiji 22). Applying this technique to 袋物 (fukuro-mono), where the body is narrower at the top like a tokkuri 徳利 (tokkuri), is challenging due to the three-dimensional shape, requiring skilled craftsmanship.
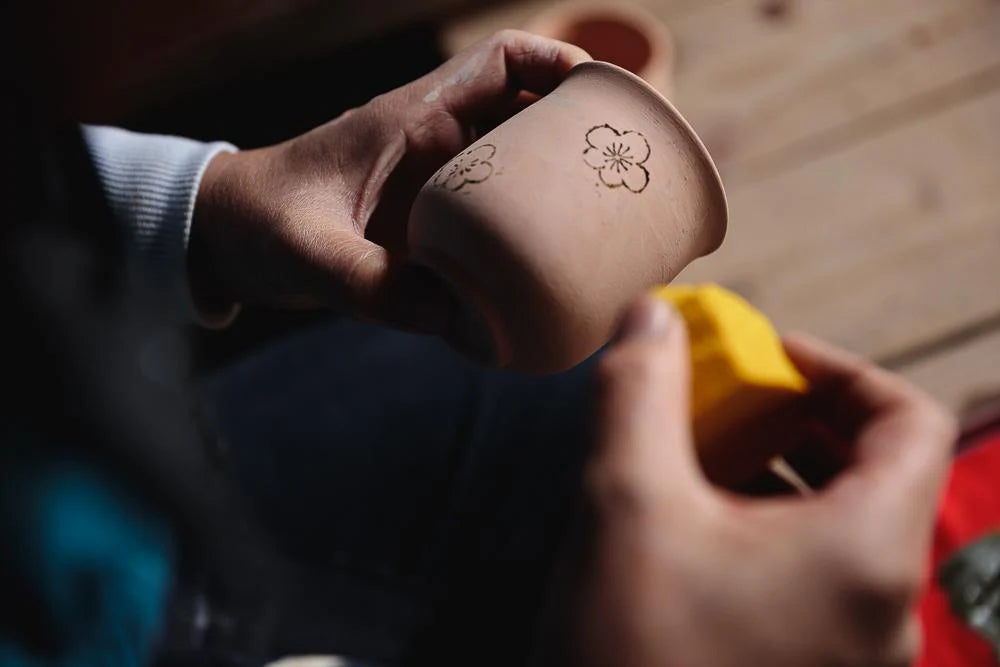
Underglaze Decoration/Painting
(絵描き, Ekaki)
Patterns like plum blossoms are stamped, or designs are directly painted with a brush. The individuality of the craftsman is reflected, resulting in expressive works. Since each piece is hand-painted, no two items are identical.
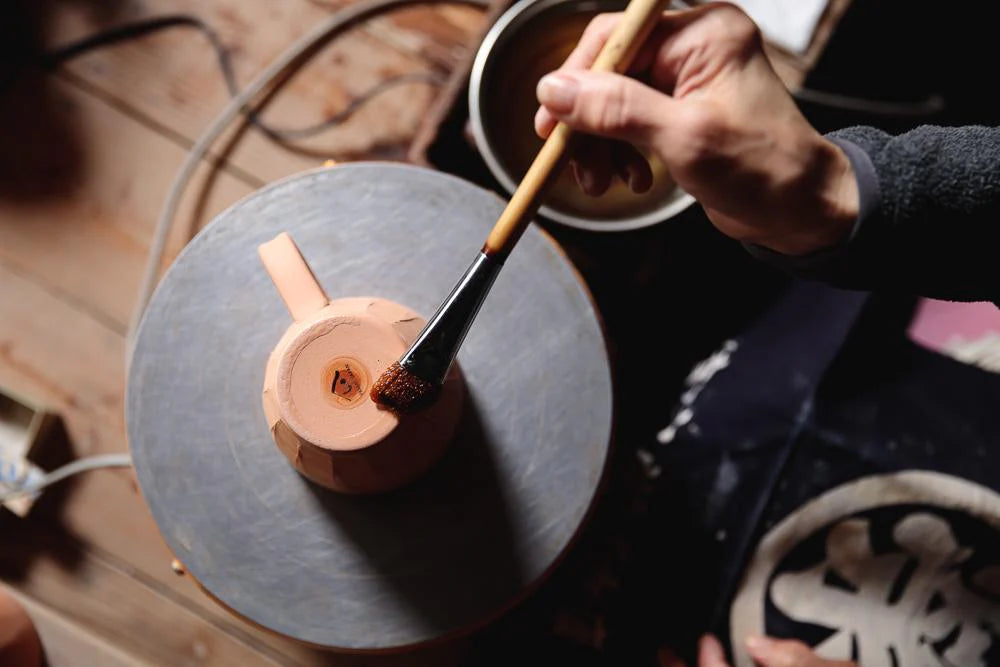
Wax Resist
(ロウ掛け, Rou-kake)
Wax is manually applied to areas where the company’s seal has been stamped or other places where the undercoat needs to be visible, to resist the glaze. These meticulous tasks create differences in the final product.
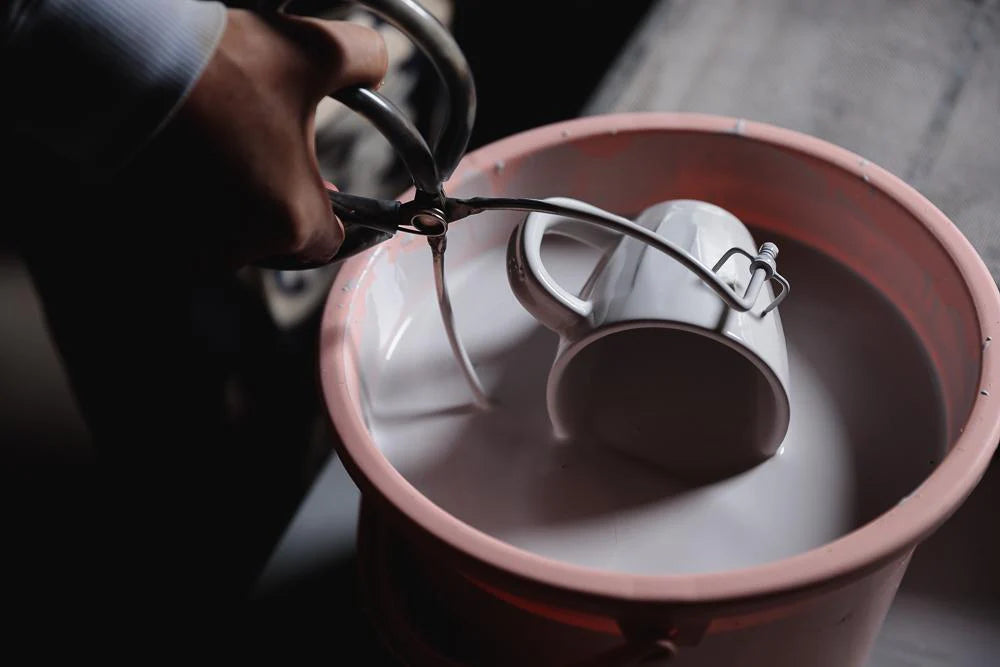
Glazing
(釉薬掛け, Yuuyaku-kake)
Once all the decoration work is finished, the glazing process begins. This is a critical step that determines the final outcome. The way the glaze (釉薬, yuuyaku) is applied, the method of removing the excess glaze, and how it is painted all contribute to differences in the finish. The ability to achieve a consistent result comes from the skilled techniques of experienced craftsmen.
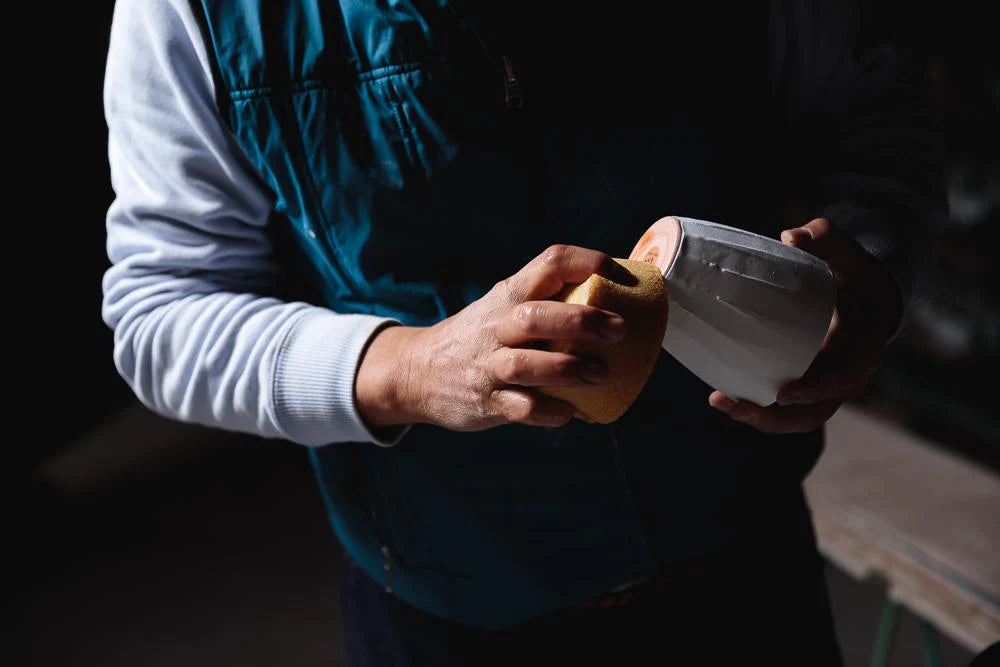
Moreover, selecting the right glaze (釉薬, yuuyaku) is crucial. The balance of stone particles mixed into the glaze and the method of application are carefully adjusted to maximize the unique 侘び寂び (wabi-sabi) aesthetic.
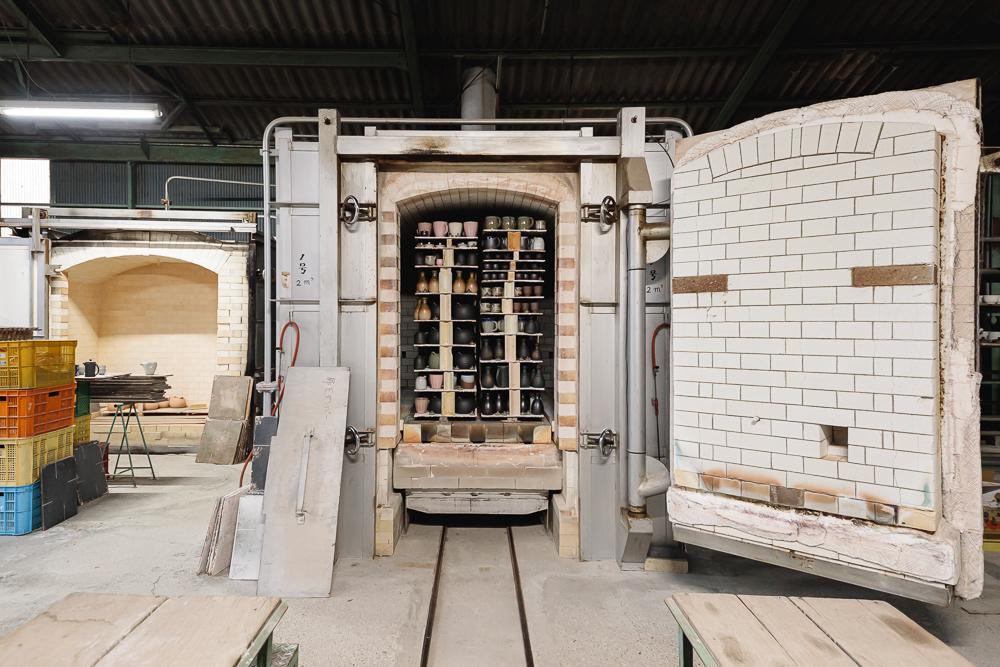
Main Firing
(本焼成, Hon-yakisei)
The final stage is the main firing (本焼成, hon-yakisei), which is the most critical process. The pottery is fired in a kiln heated to 1300°C for about 20 hours. From placing the pottery in the kiln to removing it, the process takes about two days. The final result can vary depending on factors like the distance from the heat source, the gas pressure, whether the atmosphere is oxidizing or reducing, and even the season. Usually, these various factors are carefully adjusted to achieve consistent quality, but occasionally, an unexpected beauty known as kiln transformation (窯変, yohen) occurs, resulting from accidental outcomes during firing.