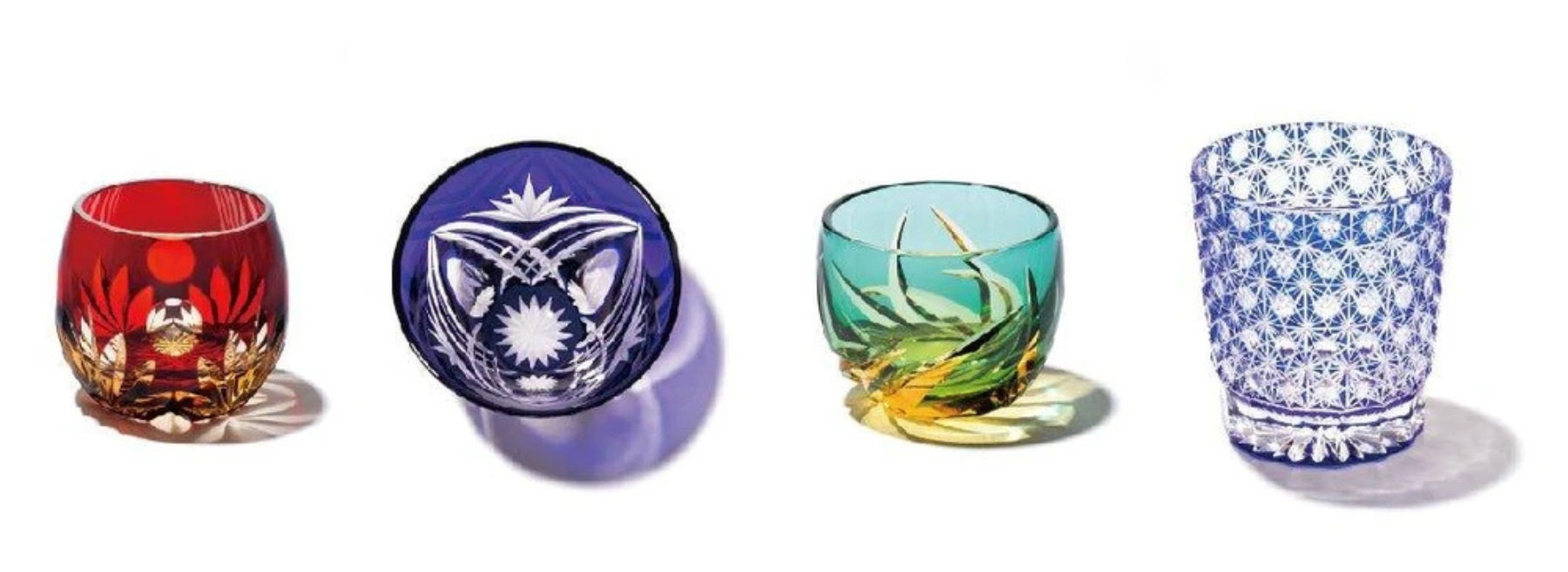
What is Edo Kiriko Cut Glass?
Description
Edo kiriko is the most famous glass craftwork in Japan. It originated in the city of Edo, Tokyo's name during the Edo period (1603-1868). Kiriko means "cut glass", hence Edo Kiriko means "Glass cut from the city of Edo". Edo kiriko sake glasses and other types of glassware are still very popular today.
Originally, patterns were cut on a transparent and colorless glass surface; however, new techniques were introduced during the Meiji period (1868-1912), when Japan first opened its doors to the outside world after having isolated itself for over 200 years. The style of Edo kiriko made with colored glass, started being produced in large quantities during this time. Today, Edo kiriko is known for its intricate designs cut into blue, red, or other colored glass. The most typical design is called nanako or fish eggs because it is composed of numerous fine, straight lines that resemble round fish eggs. However, a closer look reveals the design is actually composed of many small squares arranged side by side. Other quintessential Japanese designs include plants such as chrysanthemums or hemp leaves.
History
Edo kiriko is considered to have begun in 1834 in the late Edo period (1603-1868), when Kyubei KAGAYA, the owner of a glass wholesale firm in Edo, first tried to design a glass using emery powders.
During the Meiji period (1868-1912), as part of the government's policy of promoting Japanese industrialization, a modern glass factory was constructed. In 1881, the government invited Emmanuel HAUPTMANN, a British glass-cutting engineer, to Japan. He taught his knowledge and techniques to the Edo kiriko artisans, which led to British cut glass technology merging with Edo kiriko techniques.
Furthermore, another famous cut glass style called Satsuma kiriko stopped its production at the end of the 19th century, resulting in many unemployed artisans migrating to Edo with their Satsuma kiriko traditions. With the artisans moving in with their techniques, the method of using color coated glass was soon absorbed into the production of Edo kiriko.
From the Taisho period (1912-1926) through the early days of the Showa period (1926-1988), cut glass was called wa glass (meaning "Japanese-style glass"). It became extremely popular, and the upper classes used them for drinking glasses, tableware, or lampshades. The leading manufacturers of Edo kiriko were founded at the beginning of the 20th century and are still active today.
山田真照 Masaaki Yamada
(A brand director from Sumida-ku, Tokyo)
Design
The artist marks simple grid lines on the glass without drawing a design to provide the plan's framework. The design grid is drawn on the glass's surface using a bamboo stick or brush with red iron oxide. Next, the baselines of the design are lightly etched using a whetstone. Relying on these fine marks and lines, the delicate patterns of Edo kiriko are created with the artisan's expertise and skills.
First cuts
The base design is cut to about three-quarters of the final width and depth. The surface of the glass is cut using a sand paste-coated metal disc rotating at high speed. Generally, emery powder with many abrasive particles is used to create the sand paste. The clear pattern border lines and the irregular patterns are cut little by little. The balance between the thickness and depth of the cut lines relies upon the artisan's years of experience, as there are no detailed sketches.
Adjustments
The patterns cut in the second stage are adjusted, and the surface is smoothly polished in this process. A whetstone disc, natural or artificial, is used to cut delicate patterns which cannot be created with the metal disc used in the prior process. This is the last cutting stage to complete the designs, so careful work is required not to leave any powder residue and to ensure a brilliant finish.
Polishing
This is the final stage of production, and it is usually carried out on soda-lime glass (most prevalent type of glass). The opaque surface left by the third stage is returned once more to its original transparent state, with the attractive shine and sparkle typical of Edo kiriko. Chemical processing with hydrofluoric acid is also applied for high-class crystal glass. Depending on the piece, a variety of different polishing discs are used, such as paulownia wood discs, willow wood discs, hair brush discs, and belt discs. The final work is polished by applying water and polishing powders to obtain a glittering finish, while fine sections are polished with a cloth or a brush. To complete the final polishing, a cloth buffing disc is used to bring out the sparkle and shine of the cut glass.